How has the art of printing changed since Gutenberg? One of the greatest achievements of modern times, Johannes Gutenberg’s invention of the printing press in the mid-15th century demonstrates that printing is more than a classic handicraft but has had widespread cultural implications that persist to date. But where do things stand today? Modern-day printers operate cutting-edge, high-tech offset and digital printing machines. Their job titles range from media technology specialist to printing press operator.
Instead of wearing leather aprons, they are dressed in modern protective workwear and monitor control stations fitted with hundreds of sensors and huge screens to make sure the machines are properly adjusted to deliver optimum printing results. The number one priority of a media technology specialist working with Onlineprinters is to assure top quality of printing. To accomplish this for the several billion products printed each year, they work to defined processes and standards.
We often forget that the most important aspect of Gutenberg’s heritage is that by creating movable type he merged single elements of book production to create an efficient printing process as a precondition for industrialising the art of printing. In book printing, the industrialisation of a handicraft thus took place at a very early stage. Artistic craftsmanship was mainly about adding tasteful decorative elements such as copper engravings, etchings, lithographs and more.
Hat-trick of quality
Onlineprinters has been committed to standardising its technical printing processes already since 2006, at first mainly in offset printing which was the predominant printing technique for a long time. In 2018, the company also had its postpress operations certified including such steps as trimming, folding and binding. Since the printing industry has moved towards digital in the past years, Onlineprinters was successfully certified to PSD in June 2019 to make the hat-trick of quality certification complete, setting standards in the printing industry.
Quality expert Thomas M. Schnitzler has accompanied the company’s standardisation journey from the very beginning and visits the pressrooms of Onlineprinters on a regular basis. He commends the early standardisation efforts and he is convinced that this has set an important strategic course. Like a piano tuner, he proceeds to perfectly adjust and fine-tune the print equipment. Read our interview with the expert to learn what this has got to do with football.
Interview with Thomas M. Schnitzler
Onlineprinters-Magazine: You are an independent specialist and expert witness for the printing industry. Why is certification important for the printing industry?
Thomas M. Schnitzler: Above all, certification serves as a proof of quality to customers. It provides orientation and assures them that a certified print company has achieved a standard-compliant quality level and is capable of implementing it on a permanent basis. This is a very positive development since in the past each print shop defined itself what quality meant, leading to very different results. Therefore, independent bodies such as FOGRA have developed standardisation concepts for the printing industry to assure process stability and consistent quality. In offset printing, this is the ProcessStandard Offset (PSO) and in digital printing the ProcessStandard Digital (PSD). Both guarantee standardised processes in the production of printed products according to the international ISO 12647-2 standard series.
Onlineprinters-Magazine: What benefits do customers get from a certified printer?
Thomas M. Schnitzler: They receive printed products of consistently high quality. This is particularly important for repeated orders: If, for instance, customers print their business cards four times a year, they rightly expect that the colour should look the same each time and that the company colours are reproduced correctly. Certified print shops are capable of accomplishing this because their quality management system makes sure that the standards are complied with and that quality requirements are met throughout the entire production chain: from data acquisition through to the final product. The quality label awarded by independent bodies advertises these qualities to customers at a glance.
Onlineprinters-Magazine: Onlineprinters has completed all three certification audits. Which of them is the most important, offset printing, digital printing or postpress?
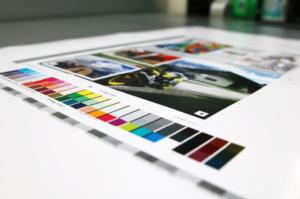
Thomas M. Schnitzler: Well, it’s a bit like a hat-trick in football: Three championship titles in a row are something very special and are the result of excellent team performance. In printing, the hat-trick guarantees the impeccable quality of the overall product. And each certification contributes to this.
Let me illustrate this with an example: A customer wants to order a large print run of an annual report. Before purchasing the whole batch, they get a few preliminary copies for a presentation to corporate management. These copies are printed digitally to keep costs low but they have to deliver the same quality in terms of colour as the subsequent large-scale offset print run. So both printing methods must be perfectly aligned with each other. Moreover, the steps after printing also need to be carried out with the utmost care and attention. Mistakes in postpress can ruin even the most perfect print. It’s like a penalty kick fail in the extra time or conceding a goal in the last minute. A football game is not over before the final whistle is blown.
Onlineprinters-Magazine: Are there any differences between certifying an online printer and a “normal” print shop?
Thomas M. Schnitzler: No, the certification procedure is the same for all types of printing businesses. Also the size of the print company doesn’t matter – apart from the fact that the certification process with its integrated quality management is more time-consuming in a large print company.
Onlineprinters-Magazine: Since when have you been accompanying Onlineprinters in quality assurance and what does this involve specifically?
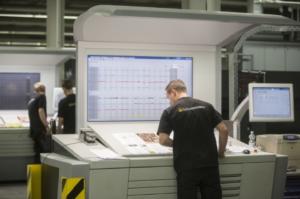
Thomas M. Schnitzler: Onlineprinters has promoted consistent quality standards in printing already since 2006. I set the whole process in motion 13 years ago – I have been with them from the beginning – when the company still went by the name of Druckerei und Verlag E. Meyer GmbH and I have continued to develop it further since. In order to achieve quality, you have to set up the entire production process: from the submitted customer data, internal data processing and printing processes to postpress activities. The employees involved in the process are a key factor: Like the players in a football team, they have to stand behind the quality promise. We educate, train and motivate them on a regular basis to assure the certified quality standards we have established to keep the team on track for success.
Onlineprinters-Magazine: How does certification affect the complaint rate?
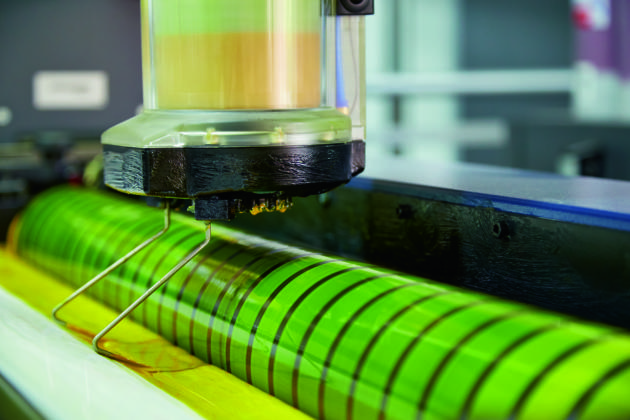
Thomas M. Schnitzler: Certification contributes significantly to recognising and eliminating errors wherever they occur. We run a highly differentiated search for the causes, and in doing so, we are able to minimise the error rate and thus customer complaints. I am not sure whether the instant replay in football is equally effective.
Onlineprinters-Magazine: What can other online print companies learn from Onlineprinters?
Thomas M. Schnitzler: Onlineprinters sets standards with its certification hat-trick and demonstrates that quality assurance and optimisation in the printing sector can lead to success. And that this requires daily training in order to work!
The interview was conducted by Elke Zapf